INTRODUCTION TO SWM SELECTIVE WASTE MANAGEMENT
SWM is in the same time a strategy and an innovative way to work.
On one hand, the strategy is focused on keeping as much separated as possible the main polluctants, like adopting separate waste collection in a municipality, instead of all waste mixed together and still to be divided/separated.
On the other hand, SWM is an innovative way to work where, in the specific need to divide multiple polluctants, it is possible to use machines designed with a very modern concept to manage the discharge of the several phases of each process, keeping separated the different polluctants and addressing them to the suitable treatment or storage point.
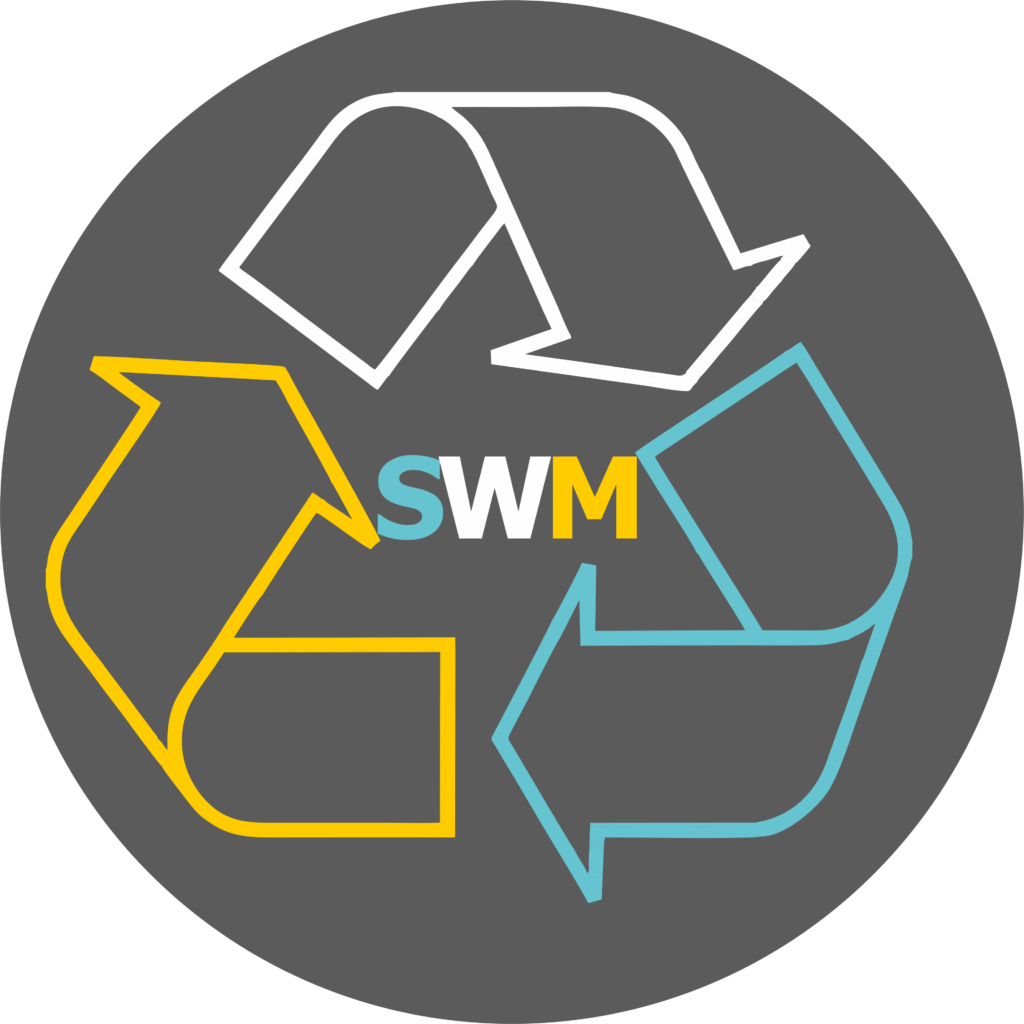
The conception of this innovative strategy has been possible combining the experiences of several leading Companies, each one strong of specific experiences, like Rollwasch for the mass metal finishing of INDUSTRIAL components, TECHNO SURFACE for the post process, surface preparation and finishing in the ADDITIVE MANUFACTURING, and some other partners pecialized in the area of waste water treatment, air filtering and similar.
But what does SELECTIVE WASTE MANAGEMENT means, in practical terms?
Is there an example usefull to understand this principle?
The replay is easy and under our eyes every day. Infact many modern villages and cities have organized in the last decades more and more selection of the waste sources, classifying them in cathegories to make easier to prepare for re-use, recycling, recovery or disposal.
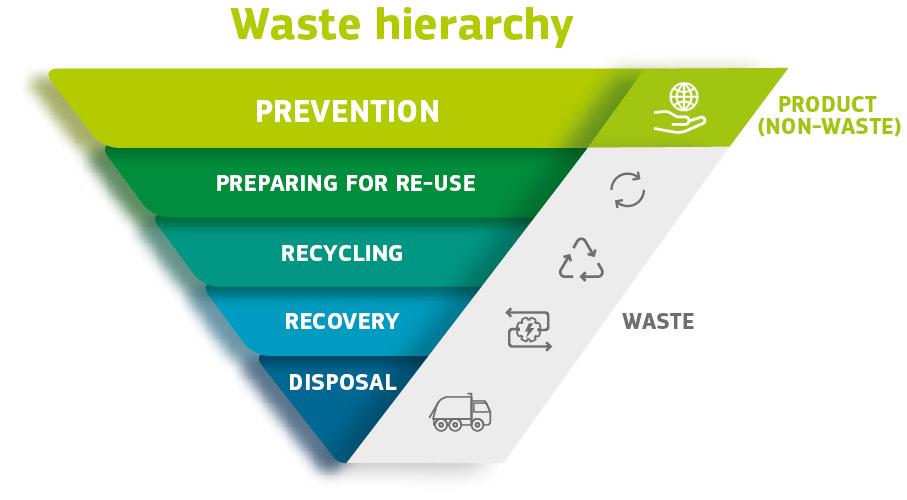
A quite similar concept has been applied to the design of a growing range of new finishing machines which are compatible with this philosophy – in few words, instead of having just a single exhaust filter combined with an outlet valve for the effluents, the machines compliant with the SWM are designed with multiple exhaust filters, combined with special automatic valves able to associate every single phase of a process with a different point to release the polluted effluents.
Just to make an example:
Exhaust filter nr 1, is associated to the first phase of a wet finishing process where a lot of oil is present on the surface of the workpieces.
The outlet valve related to this filter, is opening during all the degreasing phase, where water, additivated with a strong degreasing chemical, is removing nearby the 99,9% of fat substances,oils and grease from the workpieces, addressing the effluents all through the line 1.
After this first phase of a process has been finished, the valve of this line is automatically closing, therefore a second valve, connected to filter nr 2, can discharge just water additivated with detergent compound leaving the abrasives inside the vibratory finishing machine, to smooth actively the surfaces and make them suitable for the following surface treatment (coating, for example).
At the end, in this example, we have divided two kinds of effluents very different at all, addressing them in to completely different treatment section, one of which is dedicated to de-oiling, to recover and separate as much oil as possible;
In parallel a centrifugal filter is going to process the line 2 of effluents, recovering the mud of the abrasives and keeping in closed circuit the water additivated with detergents, with important benefits in therm of money saving and pollution reduction.
This is just an example based on two phases, but at Rollwasch we are now designing as a standard machines where up to three filters + automatic valves can be applied on a ingle bowl – at the moment starting from the minimum size of 120 liters, but in the next months also a working bowl of 60 liters with be designed.
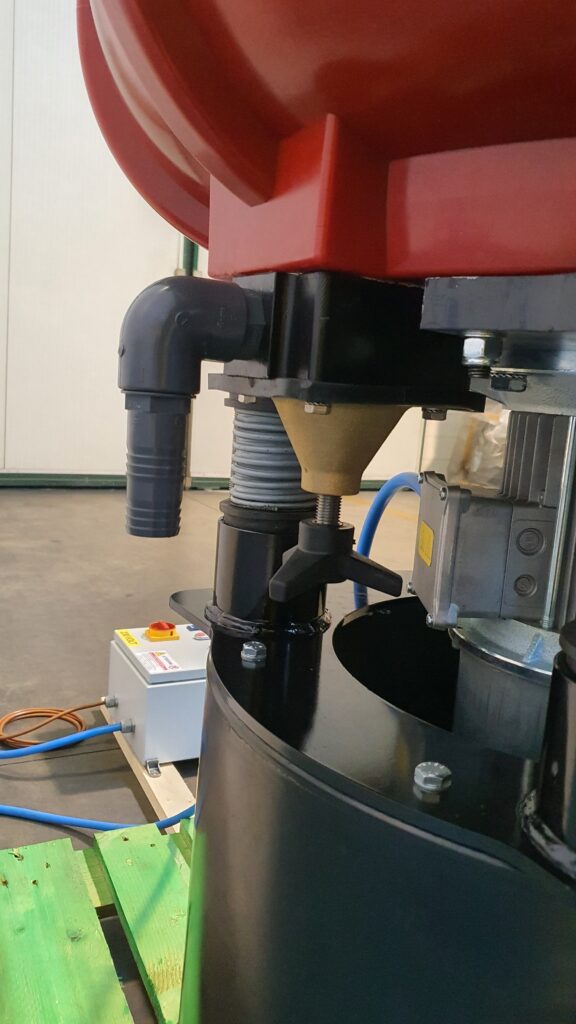
The new range SUPERMINOR SM3-D-120 can be
Equipped up to three filters and relative valves as a Standard feature.
This strategy and new way to work will be good for all kinds of customers, but for sure it will be extremely efficient in case of finishing systems composed by more than two vibratory finishing units, like 10 or 20 or more.
To know more, feel free to get in touch with Techno Surface: info@rollwasch.it
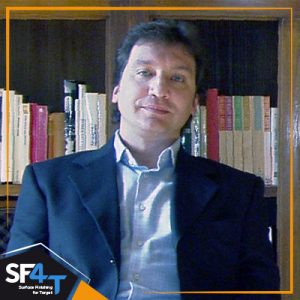
XPERT
MdM Paolo Redaelli
paolo.redaelli@rollwasch.it
CATEGORIES
Technology:
Blasting, Grinding, Media and consumables, Peening, Polishing, Post Process & Finishing for AM, PMRF, Safety, Health and Environment, Vibratory finishing
Specific category:
Vibro-blasting equipments, Vibro-Peening equipments
COMPANY
Rollwasch Italiana S.p.a.
www.rollwasch.com