Rollwasch® Italiana S.p.a. is a specialized manufacturer of vibratory finishing equipment and surface finishing systems, that in the recent years has produced several systems according to the Industry 4.0 specs, for different clients in various industrial fields.
Rollwasch® Italiana S.p.a. has growth 70 years experience in design and manufacturing also of finishing compounds and media, water treatment plants, automatic or robotic finishing systems more and more sophisticated, always aiming to the customer’s satisfaction.
The recent evolution of technologies and technical requirements in some fields like power, aerospace, medical, automotive, food systems, is inviting manufacturers like Rollwasch® Italiana S.p.a. to explore all possible High Tech available resources, to offer innovative and/or exclusive solutions and safeguards in the surface finishing field.
After a couple of years of improvements and evaluations, started in 2018, Rollwasch® Italiana S.p.a. is ready from 2020 to introduce the Lining Wireless Wear Sensors as a STANDARD reliable and innovative component of its machines and systems. Due to pandemic evolutions, this standard has been applied to STARDARD SERIES OF MACHINES with a small delay in 2021/22.
This useful innovation has been possible thanks to the partnership with the Italian Company Techno Surface SAS (www.technosurface.it), a specialist in metrology – between other activities – who has the ownership of the patent pending demand covering the use of WWS in Europe.
This technology in fact, has been designed for several different kinds of applications, where the wearing detection is required, not only for the lining of the vibratory finishing machines working bowls.
Nevertheless, in this kind of application the first Mass Metal Finishing Specialists in the world who has explored the opportunity to use the WWS and participated to its development and testing in this specific field of application, has been Rollwasch® Italiana S.p.a.
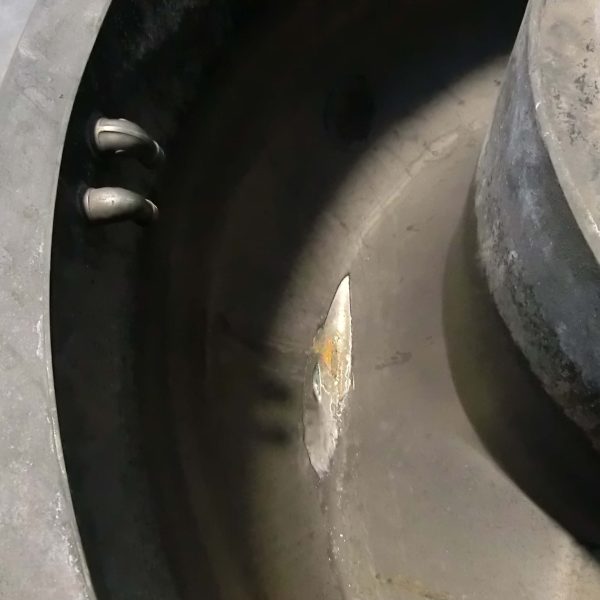
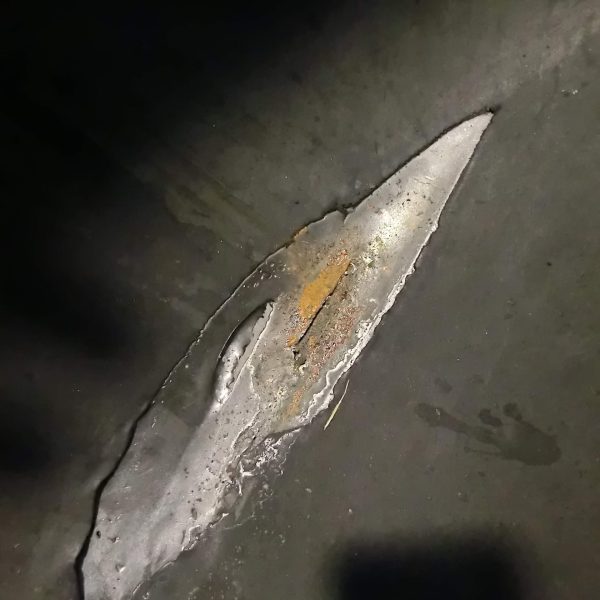
Pictures 1 and 2 show the bottom of a working bowl for vibratory finishing, where the anti-abrasive polyurethane lining has been worn out and, quickly, also the thick steel body of the bowl has been perforated by the action of the abrasives.
In 2018 the first Lining Wear Sensor has been made on a small pilot unit of about 120 liters capacity. Its technology in the beginning was composed by the exoskeleton supporting the sensors, drowned inside the polyurethane lining, at the time of pouring it in the mould (when the polyurethane is liquid, before catalysis in the oven).
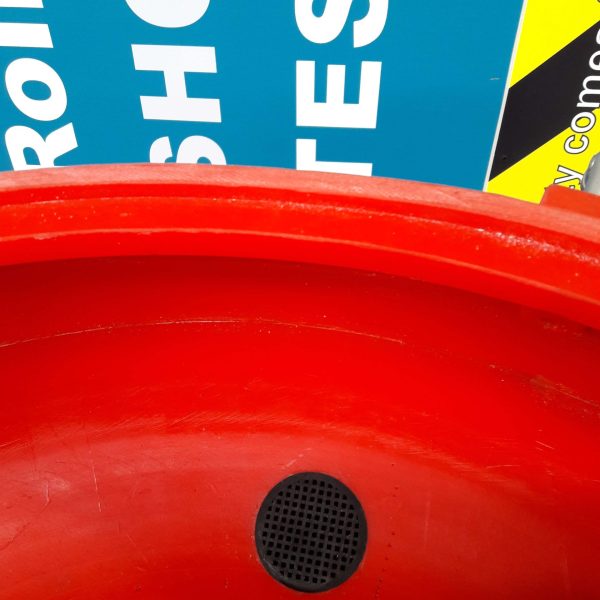
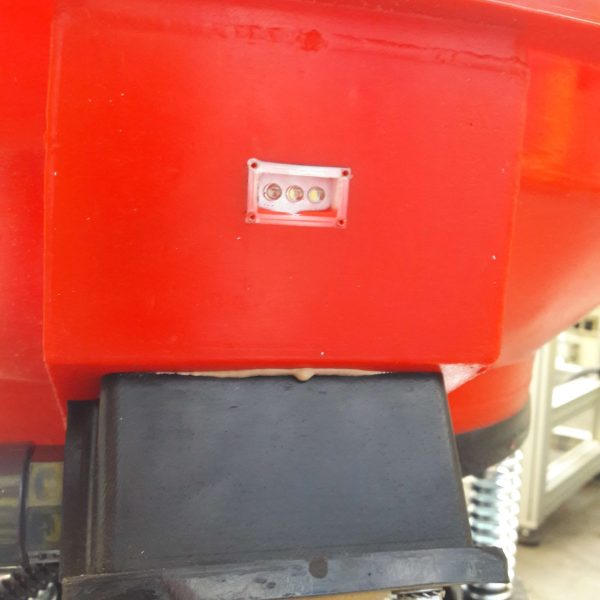
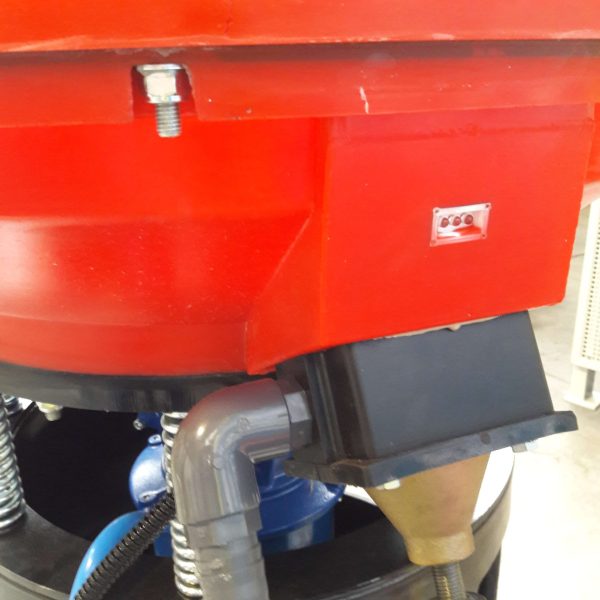
Pictures 3, 4 and 5 show, respectively: the inside exhaust-filter of the working bowl, around which it is submerged the Wear Sensor; the remaining pictures are showing the side view of the working bowl where three led are positioned to inform the status by colours: yellow = electronic circuit check ok; green = lining ok; red = lining worn-out, proceed to schedule the relining task!
What is shown in the three pictures of the red bowl, was the first step in 2018 – Then, starting from 2020 at Rollwasch® Italiana S.p.a. we are focusing to offer the re-lining after-sales service including the option of a wireless sensor to be associated to a receiver station that can be combined with an existing machine or with more units, upon the customer’s requirements.
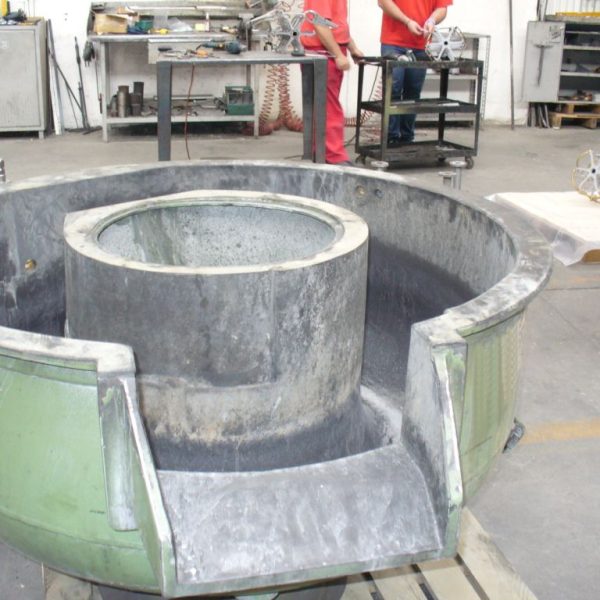
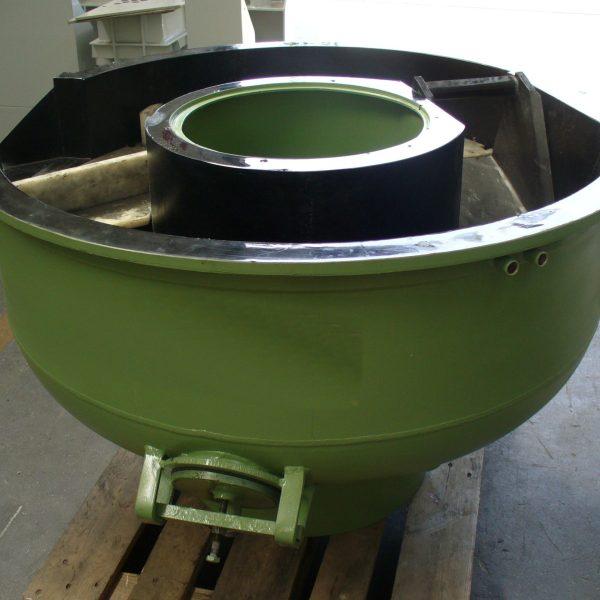
Pictures 6 and 7 show, respectively: before and after the Rollwasch re-lining service, which is offered on multi-brand basis, for the most popular brands and types of working bowls in Europe.
The exoskeleton positioned inside the working bowl, then covered with the liquid PU, remains in a very stable position inside the lining once it is hardened – therefore, as soon as a lining thick 25 mm. is worn down to 6 – 7 mm., the sensor communicates the alarm “re-line the bowl!“.
The exoskeleton positioned inside the working bowl, in this example, of an existing tank with brand different from Rollwasch®, can be connected to a “communication box”, applied externally to the working bowl. The client will receive back the working bowl with the new lining, with its communication box, and a separate receiver that can be positioned over the control board of the machine, connected to a standard 220 V plug. Every time the machine will vibrate, the sensor will automatically detect the thickness of the lining – ready to send an alarm whenever the lining thickness would reach 1/3 or 1/4 of the new original thickness.
Alternatively, in a new Rollwasch® vibratory finishing machine, the communication exchange between the working bowl and the control board will be implemented in the software of the PLC and/or in a sophisticated compatible Industry 4.0 system.
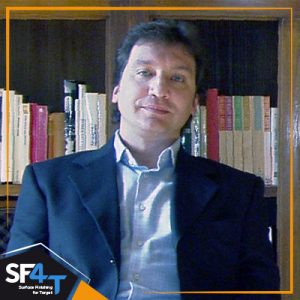
XPERT
MdM Paolo Redaelli
paolo.redaelli@rollwasch.it
CATEGORIES
Technology:
Blasting, Grinding, Media and consumables, Peening, Polishing, Post Process & Finishing for AM, PMRF, Safety, Health and Environment, Vibratory finishing
Specific category:
Vibro-blasting equipments, Vibro-Peening equipments
COMPANY
Rollwasch Italiana S.p.a.
www.Rollwasch.it