BFP is one of the columns of the Digital Platform Surface Finishing For Target that mostly represents the spirit of the platform itself. Indeed, BFP is willing to introduce to who reads the columns of Surface Finishing For Target the real soul of the information target of this platform, aiming not only to innovation, but to do it in the right direction. Therefore, eco-friendly solutions, sustainability and circular economy are the TARGET of the columns of Better For Planet.
The innovative and sustainable technology Multi Steam – Smart Color
To dye polymers it is not difficult nowadays. To submerge a volume of workpieces into a working tank, duly heated at the right temperature – i.e.: 80°C – in a liquid solution composed of 1 part of colour and 9 of water. Imagine a tank of about 30 liters – where 27 liters of water are added to 3 liters of dying colour. It can be re-used for some tasks, so it appears as a good ratio. Nevertheless, sometimes, or most of the cases, depending on what represents the final job, the colours are no more used, or used after months, even years. In many times, the simple trial for a few components, costs a lot of money due to the cost of the dyeing colors, on one hand, and on the waste dismaintling costs, on the other. A significant step forward in the practical use of dyeing colours is offered by the the innovative and sustainable technology Multi Steam – Smart Color. This technology, also called simply steam dyeing, is offering innovation, sustainability and efficiency at 360°, lets see how.
STEAM SURFING and STEAM DYEING
First of all, one of the main innovations offered by the Multi Steam technology, is to organize multi tasking finishing processes, combined with dying process in one single vibratory finishing unit. Thanks to special elastic media called “QF”, it is possible to first finish a component, then to wash and rinse thoroughly the whole mass of media and workpieces, then to start a Steam Dyeing automatic process, which is normally divided in two phases, as follows:
Steam Surfing
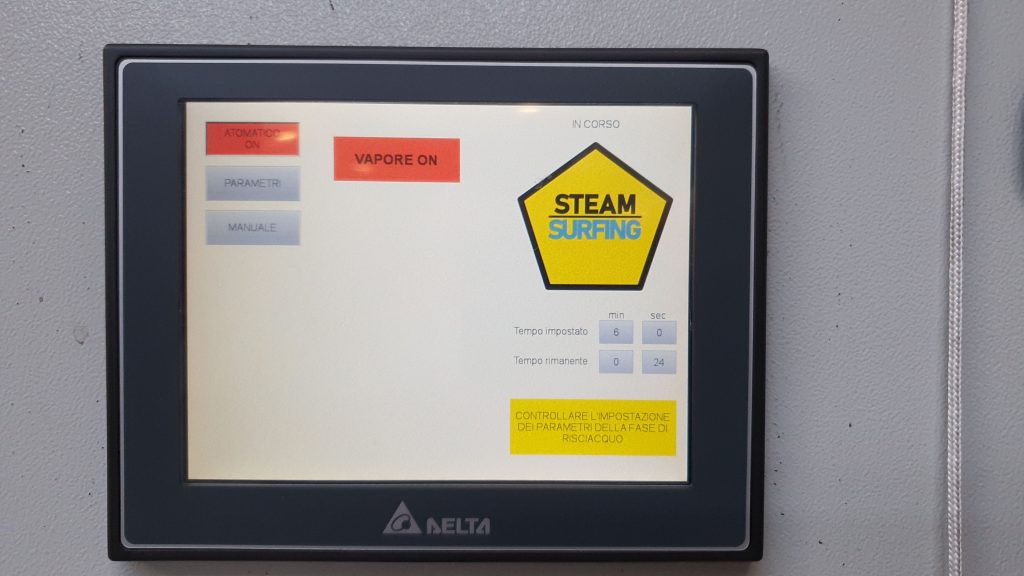
Steam DYEING
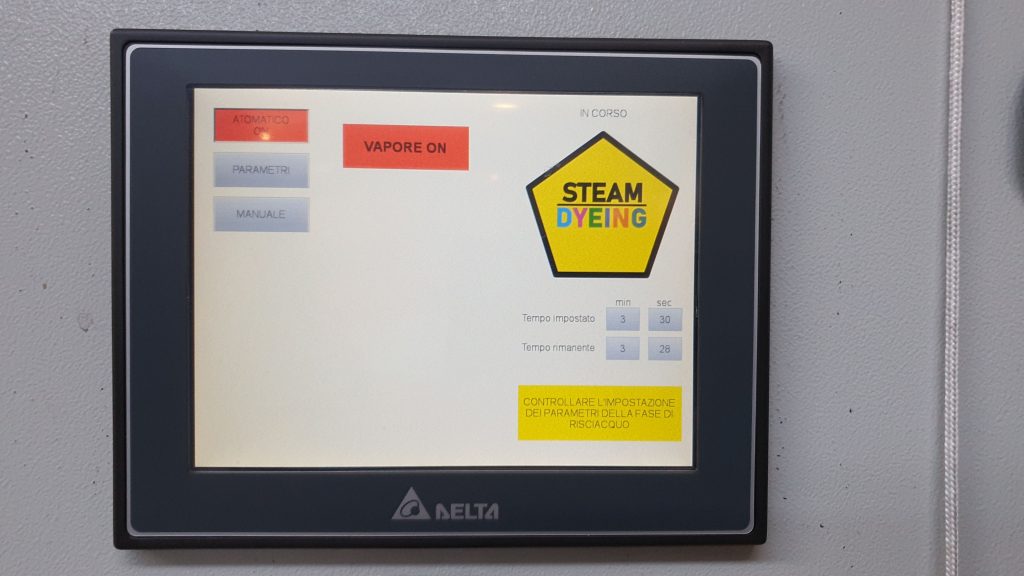
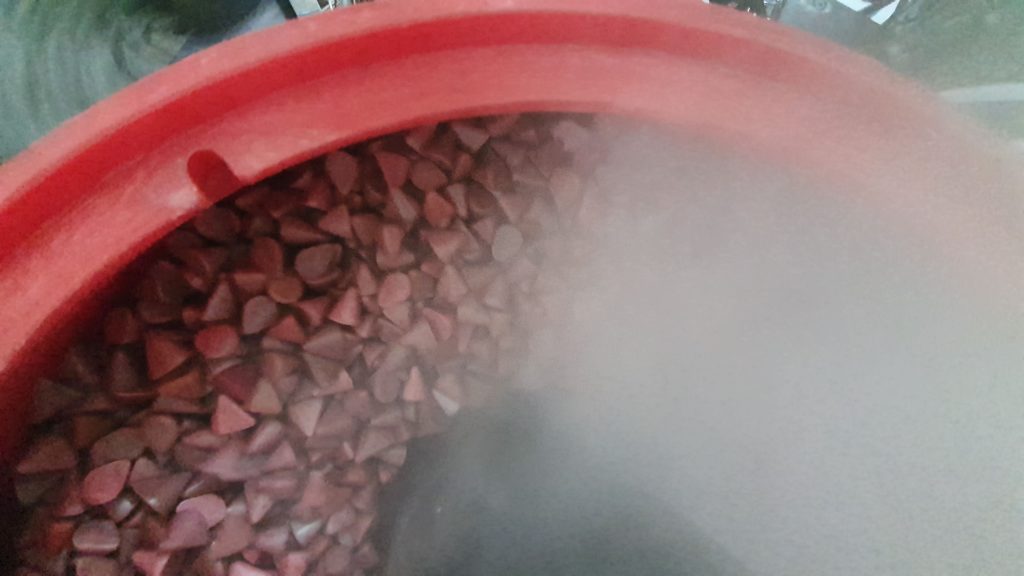
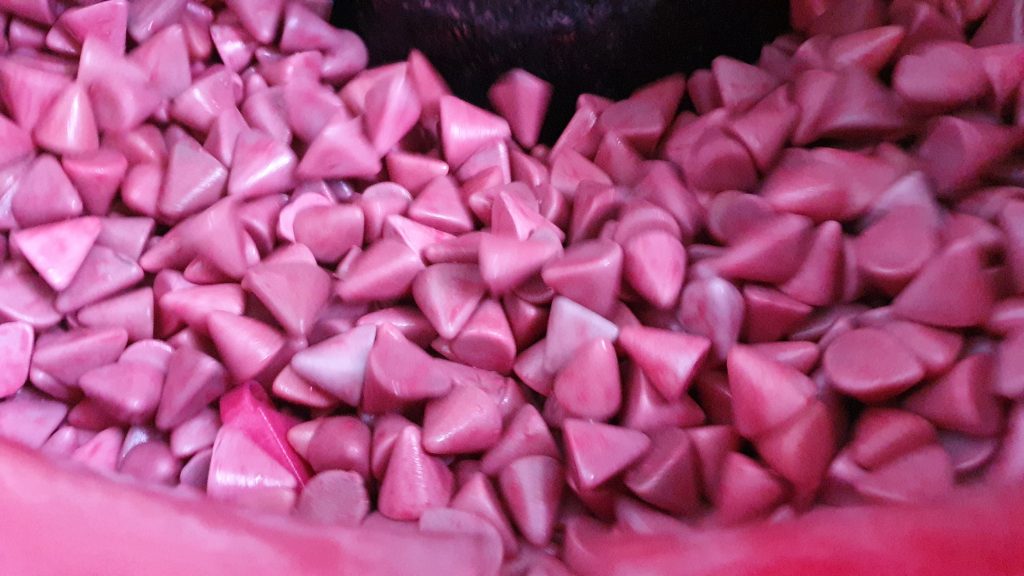
In this picture it is shown the mass of media running with few PA12 components coming from SLS – Selective Laser Sintering process.
For further information get in touch with: integram.team@gmail.com
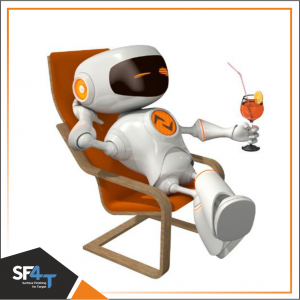
XPERT
Spencer Williams
integram.team@gmail.com
CATEGORIES
Technology:
Post Process & Finishing for AM, Dyeing, Powder recovery & selection, Surface Finishing, Unpacking or Decaking, Coating
Specific category:
Post Process & Finishing for AM; Scientific Head of R&D; Webinars & Seminars; Circular Economy Technology;
COMPANY
IntegrAM
www.integram.eu