3D printing – otherwise known as Additive Manufacturing – is around since the early eighties, but it took around 15 years for this groundbreaking technology to find its way out from the universities and research centers, with the rise of future giants like 3D Systems, Stratasys, and EOS.
Almost 40 years after those pioneering times, as of today, we have AM technologies capable to print at production-grade speed thermoplastics, metals, embedded electronic circuits, and even biomaterials, with sizes ranging from rocket engines to one-micron resolution microscale objects.
Furthermore, the costs of embracing additive manufacturing are constantly decreasing, moving toward its natural democratization. And as co-founders of Norge Systems, the maker of the first low-cost SLS® 3D printer, we are happy and proud to have been accelerators of this trend.
High throughputs – suitable for single-shot to medium-run manufacturing needs, finally affordable technologies and wide material choices: these are the reasons why the userbase of industrial and professional 3D printers is growing at an exponential rate.
The advantages of AM compared to other production means are many, but in this article, we want to concentrate on the environmental aspects.
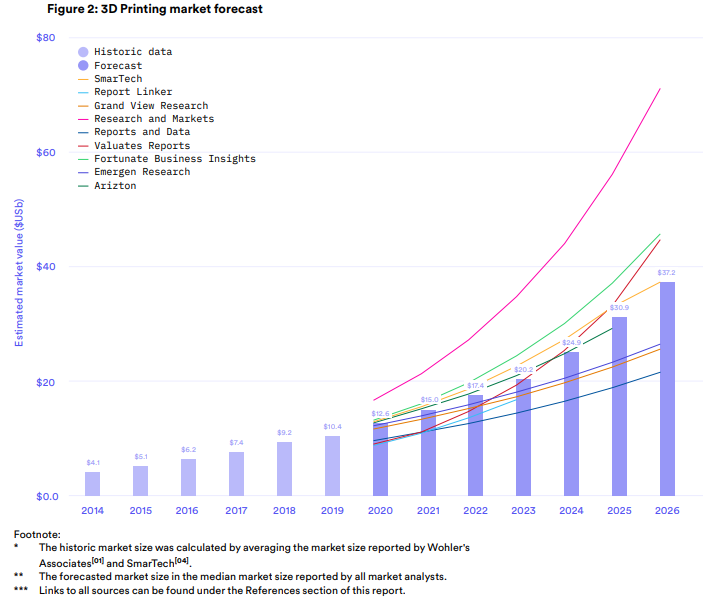
Photo courtesy of 3D Hubs
Naturally sustainable, economically convenient
Can we consider additive manufacturing environment-friendly? Compared to other production technsologies, mostly subtractive, the answer is yes: 3D printing is naturally more sustainable. In essence, it is because you fuse, melt or deposit only the material that will form your object, with the exception of some supports that you will have to remove afterward; clearly more convenient than milling or turning your object starting from a larger blank. The economic and environmental advantages are clear, even without considering the costs and ecologic impacts of the disposal of special waste, which is bigger for subtractive processes due to the presence of lubricants in the scraps and shavings. Furthermore, AM gives designers new levels of freedom, allowing the design of shapes and volumes not possible to achieve with CNC machining, and use generative design and topological optimization to reduce the part weight and raw material needs while keeping consistent mechanical properties.
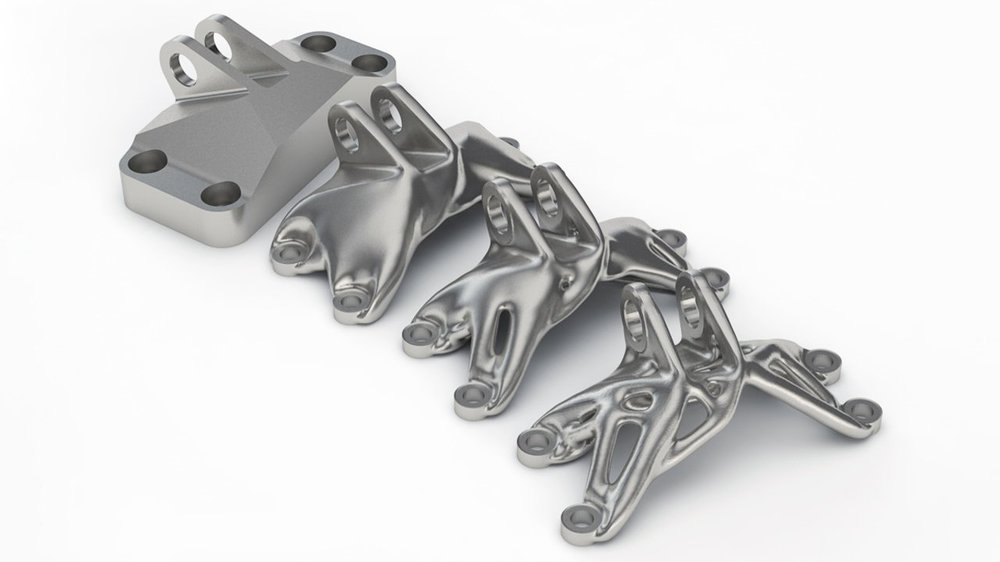
Photo courtesy of Engineering
Reducing global energy consumption
Whether it’s generated by nuclear or fossil fuel-burning power plants, electricity plays a major role in the ecology impact of manufacturing activities. But taking into account only the energy needed to run your milling machines or 3D printers can be misleading, and shows only a part of the global picture. In this interesting chart (courtesy of Amfg) we can see the huge differences between CNC and metal A.M.
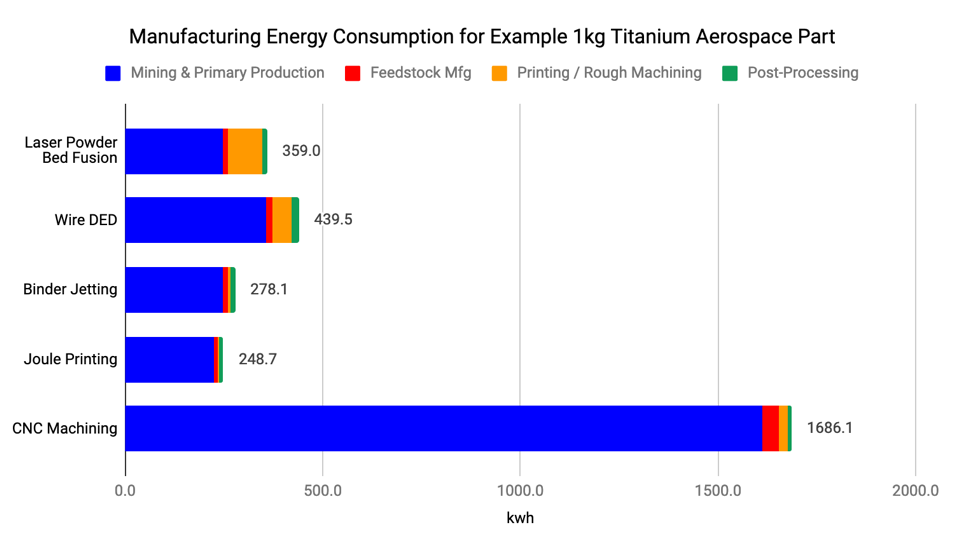
It’s clear that, even for a notably energy-hungry technology like Powder Bed Fusion, the global kwh cost to manufacture 1kg of titanium is almost 5 times less than CNC.
Product development and environmental impact
Even if not obvious as the previous example, there is another factor that makes AM so performing from the sustainability point of view: shorter time to market. From the first sketch to the final design of a product, the number of tests that have to be carried on to get there can be… a lot. And if you plan to manufacture your product, for example, with injection molding, you will have to design and manufacture (through CNC machining) as many molds as the design iterations you have to evaluate. As aforementioned, machining is generally a less green option than AM, and in the case of CNC outsourcing, we also have to take into account the road transportation of the molds from the supplier to the testing facility, which means fuel and rubber consumption, plus air pollution. And the disposal of the molds that will get discarded. With additive manufacturing, you can print different design iterations of your product virtually in one shot, select the prototype that better fits your need, and manufacture via CNC only the final mold. And most of the time you can directly 3D print your parts at your facility, reducing the fossil footprint and time. It’s a known story that thanks to 3D printing, Ducati was able to cut by 20 months the development times of their Desmosedici race bike: it took only 8 months instead of the 28 months needed for the previous bike, developed with traditional methods. So even when is not used to manufacture end-use parts, 3D printing helps shorten the development cycle of a product, dramatically reducing its ecological footprint as well as the costs.
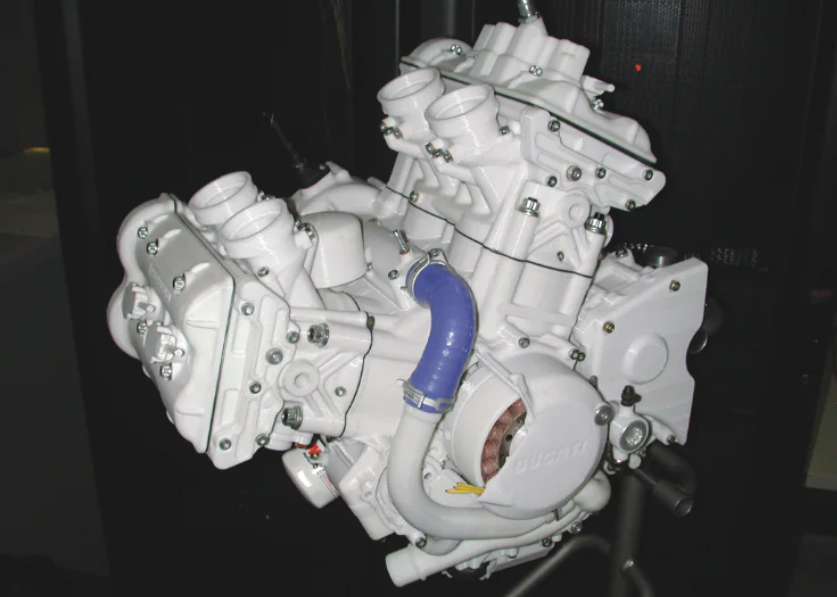
Photo courtesy of Ducati and Stratasys
A new trend: Ecologic materials
In the last years, many companies started to develop eco-friendly materials for 3D printing, using recycled or non-fossil raw materials. For example, we have now recycled scrap metal powders from Molywork, and filaments made of organic minerals and PLA from Polyterra. Fun fact, the great old bio-sourced materials is Nylon 11 – developed in the 1950’s, way before A.M. and this new eco-trend – and widely used since then for many applications. It’s produced from castor beans, and it’s the only non-fossil thermoplastic that can be used on Laser Sintering 3D printing and MJF systems.
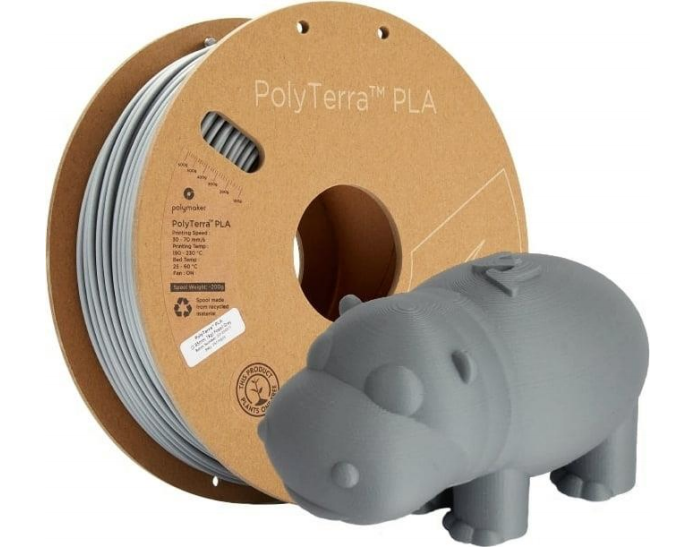
Photo courtesy of Polyterra
Polymer powders: recovering as much material as we can
Powder bed technologies like SLS and MJF put the reusability of the material at the core of their manufacturing logic. For those who is not familiar with these technologies, basically, the plastic powder serves both as support material (unfused) and as build material (fused). Once your 3D print is ready, you take out the parts from a big “cake” of powder, clean them with a bead blaster, finish them with a tumbling system if needed, and you’re ready to go.
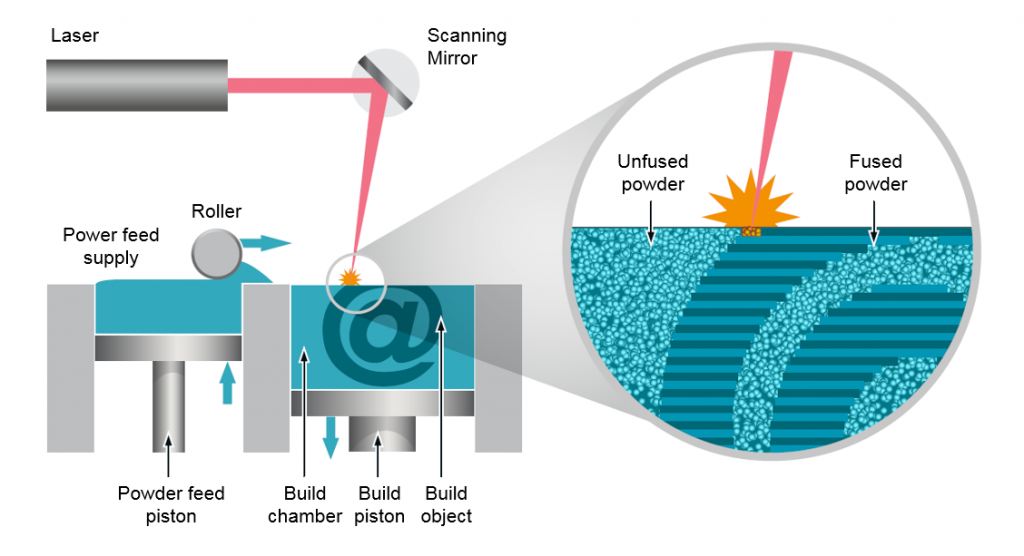
But what happens to the “cake”? Well, that used powder gets sieved and mixed, often manually by a trained operator, with varying percentages of new powder, and then reused for the next job. So, differently from other technologies where the supports need to be cut and trashed, with SLS and MJF everything gets recovered with notable economic and ecologic advantages. Automatization of this part of the process is something that – as 3D printer manufacturers – we always looked forward to. This is why we were enthusiast to cooperate – as part of the IntegrAM Group – in the development of the new DCK 01, the first fully automatic post-processing tool for powder-based 3D printing systems. Besides parts cleaning and finishing (no chemicals needed), the Group put a lot of effort into making the powder recovery system as efficient as possible, and without the need of manual intervention by the operator. Our goal was to have a tool capable to reduce powder waste while ensuring a clean and safe working environment, for improved sustainability. And we did it.
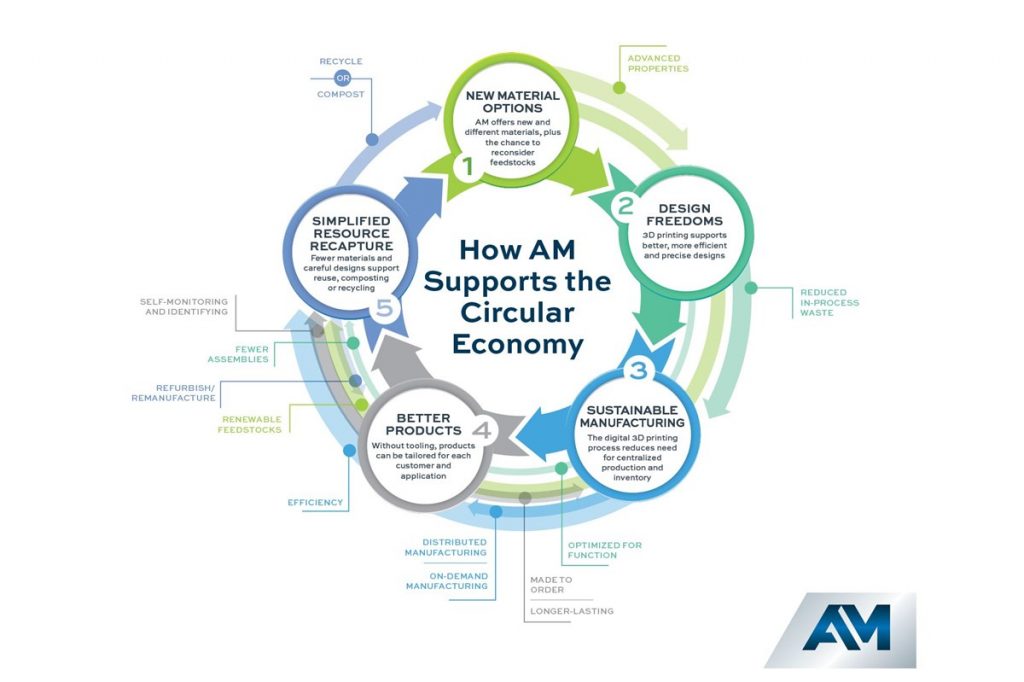
Photo courtesy of Additive Manufacturing
Cross-technology circular economy
Recycling material is part of the circular economy flow, and this applies also to additive manufacturing. Even with SLS and MJF technologies, where powder gets reused many, many times, after a certain number of cycles the material is no more suitable to be used to print parts. Nowadays, exhaust nylon powder is used to manufacture filaments for FDM printers, and there are some ongoing tests to use it as filler for construction materials.
The target is to reduce furthermore the already small ecological footprint of AM.
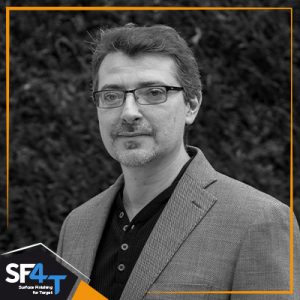
XPERT
Alessandro Facchini
a.facchini@spengler.tech
CATEGORIES
Technology:
Engineering & Consulting, Post Process & Finishing for AM, Training & Test Center
Specific category:
Vibro-blasting dry equipment*, Engineering, Technologic Consulting, Training Centers, Unpacking or Decaking.
COMPANY
Spengler SAS
www.spengler.tech